PRESSING INSTRUCTIONS (with a VIDEO) for PNW PRINT CO's DTF TRANSFERS
- Elena Duggan
- Aug 24, 2022
- 5 min read
Updated: Jun 2
For best results, it is recommended to use a commercial-grade or heavy-duty press. These types of presses provide the necessary even and adequate pressure required for successful DTF transfers.
Hobby presses like the Cricut Easy Press, HTVRont, inexpensive machines from Amazon, or combo many-in-1 presses will not yield the same results.
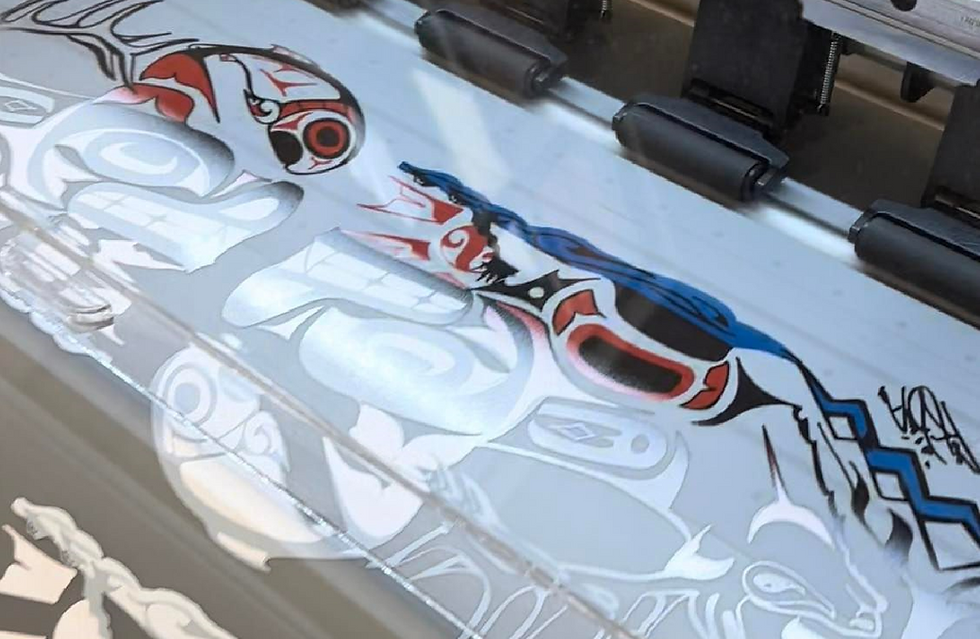
We provide free samples of our DTF transfers with your orders so you can ensure compatibility with your heat press settings before working on your order. It is essential to conduct a test before proceeding to ensure optimal results.
Our DTF transfers can be applied to a variety of materials, including cotton, cotton/poly blends, tri-blends, polyester, nylon, leather, vinyl, denim, canvas, and even wood. Settings vary.
Unlike other transfer methods, our transfers minimize or prevent scorching. They are applied at a lower temperature range of 250-280 degrees (see detailed instructions for each material below) for just 13-15 seconds (initial 8-10 sec of press + 5 sec repress). This contrasts with other vendors' settings of 300-320 for 20+20 seconds, HTV transfers that require 315 degrees for 60 seconds, and sublimation transfers that require 380-400 degrees for 50-90 seconds.
DTF HEAT PRESS SETTINGS
Please note that press settings may differ for each individual machine and material. Use the provided samples to find the appropriate settings for your press.
Here are some general guidelines to consider:
Garment pre-pressing is not required for DTF transfers as moisture is not the enemy of DTF, unlike sublimation. You may pre-press if your garment is wrinkled.
Set the pressure to HIGH or 60-70 PSI (or setting 6-7 on Stahl's Hotronix, PNW Cascadia Pro, and some HPN presses).
Set the temperature: it depends on the fabric content - see suggestions below.
Place the transfer with the adhesive side facing down. If you don't have a cover on your upper platen - cover the transfer with parchment paper to prevent it from sticking to the upper platen due to static electricity.
Press for 8-10 seconds.
To enhance adhesion for intricate details, use a folded microfiber towel to rub the film all over immediately after opening the press, pressing the fine lines into the fabric. Pay close attention to sharp corners and fine design elements while rubbing.
For the hot peel method, swiftly remove the film in one continuous motion while it is still very hot. Do not pause or stop mid-peel and avoid pulling it upwards. Always pull away. Refer to the video below for a proper technique.
For the cold peel method, remove the garment from the press and allow it to cool completely. Once the garment is cold, remove the film in one smooth motion. Avoid pausing or stopping mid-peel and pulling the film upwards. Always pull away.
For optimal results, we recommend a second press: re-press the garment for 5 seconds using Kraft paper or another cover sheet of your choice, with high pressure.
These recommendations should help you achieve the best results with your DTF transfers.
PRESSING SUGGESTIONS
COTTON & POLY-COTTON BLENDS
Set the temperature to 265-275°F. Press for 8 seconds. Re-press for 5 seconds with Kraft paper.
Hoodies may require a slightly higher temperature range of 275-280°F. Press for 10 seconds with medium-to-high pressure. Re-press for 5 seconds.
Material with higher polyester content and other non-cotton fibers: use the lower end of the temperature range to prevent scorch marks.
NYLON & 100% POLYESTER
Polyester settings can vary greatly – TEST FIRST. To avoid creating a pressed box look, try using a temperature range of 250-260°F for 7-8 seconds. The pressure can be lowered to medium-high or 50 PSI.
For nylon, TEST with temperatures around 245-255°F for 5-7 seconds. The pressure can be lowered to 40-50 PSI.
To improve adhesion to 100% polyester and nylon:
place a thin cotton kitchen towel or an old cotton shirt underneath your shirt.
use a folded microfiber towel to rub the film immediately after opening the press. Pay close attention to sharp corners and fine design elements while rubbing.
You may have to allow the garment to cool completely and peel the transfer COLD for better adhesion.
Repress for 3-4 seconds.
MISC. MATERIALS
Generally, thick fabrics require slightly higher heat settings.
For baseball hats: when pressing baseball hats made of polyester, it is essential to apply good pressure. We tested using Stahl's Hotronix 360 press. Recommended settings are 270-280°F for 6-8 seconds. It is recommended to perform a cold peel: remove the hats and allow them to cool completely before peeling and repressing.
For items like umbrellas, stadium chairs, and rain jackets: testing and trial-and-error are necessary for these types of items. Start low.
Regarding clothing dye migration: some clothing dyes may migrate to the transfer. To check for potential migration, perform a 24-hour test. If dyes migrate, the regular DTF transfer may not be suitable for you. Seek out special dye-blocking DTF transfers. Unfortunately, we do not offer these specialty transfers.
TRI-BLENDS AND ANY OTHER HEAT-SENSITIVE MATERIALS
Rayon fiber is very heat and pressure sensitive. Turn the heat down to 250-255 and pressure to medium to avoid scorch marks. Do not pre-press. Press the transfer for 5-7 seconds, hot peel, and re-press for 3-5 seconds.
Keep your seams off the platen as much as possible. Use small size lower press platen if your press has interchangeable platens. Or, use pressing pillows to elevate the garment.
FINISH IDEAS
For a matte finish, use the back of an old t-shirt, butcher paper, or Kraft paper (think absorbent or textured material) when re-pressing.
For a semi-gloss finish, use a Teflon cover sheet or parchment paper (think non-absorbent or smooth material) during re-pressing.
For a matte, visibly textured finish, use a piece of duck cloth—it's our favorite finishing method! It helps press the transfer into the fabric fibers and creates a beautifully subtle, textured look.
TROUBLESHOOTING
TRANSFER DOESN'T STICK OR RIPS APART WHEN REMOVING THE CARRIER SHEET
Please review the proper technique in the video posted above.
HOT PEEL DOES NOT WORK
To ensure a successful hot peel, there are three crucial requirements: adequate heat, time, and pressure.
Proper pressing temperatures are important! Use an infrared thermometer to scan the upper platen of your press. This will help identify any cold or hot spots and ensure that the platen's temperature matches the temperature displayed on the press's screen.
Peel while still very hot. Hot-peel films don’t perform well when peeled warm—but they do peel well when cold.
Hotter and longer is not always the answer! Pressing at too high a temperature or for too long can lead to overcooked transfers that feel stiff, don’t adhere properly, and may not last as long. Always follow our recommended temperature and time settings for the best results.
If your design includes sharp corners or intricate, thin details, try this workaround: as soon as you open the press, rub the film with a folded towel—making sure not to shift the transfer’s cover sheet—while pressing the transfer into the fabric fibers. Then, allow the garment to cool completely before peeling. After peeling, re-press the garment as usual.
Hot peeling may work just fine, but be sure to test it first.
If your press can’t provide even, heavy pressure, you can follow the same workaround described above. However, please note that if the initial pressure is too low, the transfer may wrinkle and begin to crack or peel after just a few washes. Be aware that some clamshell presses are known for uneven pressure distribution.
FILM STICKS TO THE UPPER PLATEN AND RIPS MY TRANSFERS
Film sticking to the upper platen can be caused by static electricity, which is more likely to occur in low-humidity environments. To avoid this issue, use parchment paper on top of your film.
Furthermore, wearing shoes with rubber soles while pressing can help dissipate static electricity buildup.
If you have any additional questions, please email order@pnwprintco.com.
Thank you!
Danny & Elena @ www.pnwprintco.com
PNW Print Co. is not responsible for operator or machine errors when applying DTF or sublimation transfers. We recommend purchasing extra for each transfer and practicing with your machinery, temperatures, pressure, and times before attempting your final product.
Comments